Contents
The coronavirus (COVID-19) is not only a health threat but is also a potential global- businesses disruptor, posing a considerable risk to the entire world economy. Here, I talk about the impact of the COVID-19 and how some American companies are dealing with this outbreak.
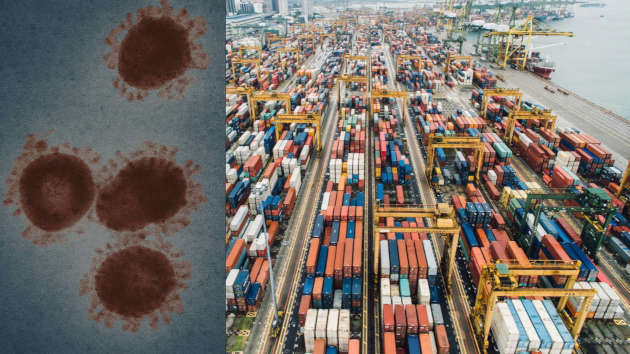
Overview of Supply Chain Disruptions
Every day, supply chains continue to be exposed to increasing levels of operational risk. Several human-made and naturally occurring events threaten to delay or disrupt business operations. According to the recent annual risk report from DHL Resilience360 (2019), a supply chain management risk-management software platform, supply chain disruptions are increasing 23% year over year, costing businesses tens of millions of dollars of loss revenue.
How is the coronavirus disrupting supply chains?
The latest threat is the global spread of the coronavirus. The outbreak is beginning to disrupt the supply chains of top production countries, which include; Brazil, Canada, China, India and the United States.
Businesses are beginning to feel the impact of this latest threat as the Dow Jones Industrial Average experienced a one day drop of 1,000 points due to increasing coronavirus fears. This was the third-largest daily drop in the Dow’s 124-year history.
With so many countries being impacted by this virus, global and governmental health agencies are taking swift action to contain and reduce its spread. These actions include the quarantining of activities and those located in geographical regions affected by this virus. Often this includes stopping production and movement of goods in the supply chain that are critical to a firm’s customer market and its revenues projections.
How is one American business handling coronavirus supply chain disruptions?
Recently, one of our valued employer partners of the MS in SCM program provided details to students on how the virus is affecting its customers, business and supply chain.
In the course of fulfilling customer orders, execs realized that a key component needed in their products is manufactured under a single-sourcing agreement with their production partner located in Wuhan, China. Due to the outbreak of the coronavirus and the response by Chinese and global health officials, their production site is now idle.
The situation has left the company without access to inventories of this component. After depleting existing inventories to fulfill current customer orders, the company has turned to secondary inventory sources of remanufactured components to continue production and order shipments.
Additionally, customers impacted using remanufactured components are being notified and guaranteed these parts will be replaced once the Wuhan plant is operational.
While this solution is part of the employer partner’s supply chain risk-management strategy, it is delaying the shipment of customer orders. Also, the disruption has increased supply chain costs related to the sourcing, use and later recall of remanufactured components to meet customer service guarantees. At present, the company estimated this could run into hundreds of thousands to millions of dollars in additional cost, depending on the length and severity of the effect of the virus on global business.
What should supply chain professionals do?
Today, supply chain professionals need to develop agile and robust supply chain operations able to mitigate the risks posed by events such as the coronavirus; disruptions like these threaten the entire supply chain network. By performing regular risk management analysis and periodic testing of risk-management plans, supply chain managers can be more confident that their supply chain operations can withstand the occurrence of a risk event. Preparedness will ensure the company faces minimal disruption and that it will have sufficient time needed to return to normal operations.
A website has been launched to serve as a hub for all UT Dallas information on the coronavirus outbreak and will be updated periodically with new information as it becomes available.